Dat met die rubber kan werken, de hardheid van je rubber (shore-klasse), gaat veel bepalen. Ik heb eventueel nog klemvoetjes van een testopstelling met een stuk schroefdraad en een rubber uiteinde. Twee moeren erop en een beugeltje en je kan misschien rechtstreeks drukken daarmee
Dank voor je blijvende steun en tips. Zoals besproken, zie ik voorlopig op het gebied van de messing vervorming enkel doodlopende wegen. Om diverse redenen werken de diverse technieken niet (materiaal te dun, rubber niet buigzaam genoeg, te weinig kracht op de 'pers' et cetera. Ik ga terug naar het originele plan, vacuforming, met een beter actieplan. Mocht dat onverhoopt niet lukken (hoewel ik hier nu toch wel enige hoop op heb) en ga ik terug naar metaal, dan zal ik je suggesties meer in detail bestuderen.
Onvoorstelbaar welk werk hierin gestoken wordt
Dat begin ik wel met je eens te worden. Het is vooral bijzonder frustrerend soms, zoals gisteravond. Ik geef niet snel op, maar als alles wat ik probeer nét niet werkt en nét niet goed genoeg is, geeft dat weinig motivatie. Dan moet ik het werk echt neerleggen en er een nachtje over slapen om weer verder te kunnen.
de volharding zal zich vertalen in een supermooi model, hoedje af.
Daar hoop ik dan op. Dank je voor de steun.
Ongelooflijk wat hier verzet wordt voor een band![]()
Yep.
Zelf was ik al heel tevreden met mijn resin exemplaren (boven) welke ik gecast heb met een Esci/Italeri als master.
Ziet er meer dan deugdelijk uit inderdaad! Ook het geschilderde exemplaar is zeer overtuigend en fijn. Ik heb vandaag een dikker microzaagje gekocht waarmee ik de bestaande mal eventueel kan aanpassen. Ik ga verschillende dichtes uitproberen en die dan gieten.. kijken hoe het wordt. Dan pak ik de meest overtuigende. Wat de bandjes betreft heb ik vrij goede hoop op succes.
Om rust te krijgen in het proces, een hydraulische krik gebruiken
Om kort te zijn; theorie: wellicht; praktijk: nee. Laat ik het als aller-allerlaatste poging opschrijven. Ik mag hopen dat dat niet nodig is. Ik snap het idee wel en ik vind het ook knap bedacht, maar in beginsel niet voor deze huishouding weggelegd.
In dit geval komt zelfs het idee om iets als Clever Putty te gebruiken bij mij naar boven. Je heb de ondermal, en daarin een hoeveelheid Clever Putty, als bolletje persen. In koude toestand, als deze moeilijk te kneden is. Een tekort aan Putty kan je opvangen door de krik te lossen en een bolletje op de bestaande Putty te leggen
Dat lijkt een werkbaarder idee. Ik heb die putty hier liggen, heb 'm alleen nog nooit gebruikt. Hij is inderdaad goed stevig, meer dan bijvoorbeeld Blu-Tack waar ik ook al naar had gekeken. Wellicht... maar ik hoop echt dat het vacuformen nu gaat werken.
100. Een van de diverse pogingen... 'forceren' op de draaibank.
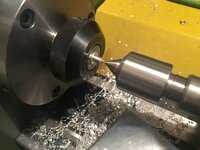
Het messing is te dun. Nog een dikker stuk geprobeerd... weer te dun.
101. Volgend plan is, zoals gezegd, weer vacuformen. Er moest een nieuwe mal gemaakt worden. Te beginnen ditmaal met het tappen van een gaatje. Dit is een foto van een teststukje. Ik heb een boortje van 1,75mm. gebruikt en dan een tapsetje M2. De diameter wordt dan 2 millimeter, waar 2,41mm. vereist is. Ik had helaas alleen M3 en moest dus naar de ijzerhandel om een M2-set te halen.
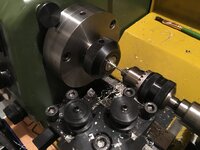
102. Hier wel het uiteindelijke werkstuk (nog te vormen natuurlijk). Het gat is hier getapt en het schroefje past. Dat laatste viel me, na diverse tegenslagen, nog alleszins mee.
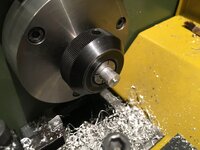
103. Toen de mal gevormd was aan de vacuform-kant, draaide ik het stukje om in de spantang en sneed ik het overschot er vanaf.
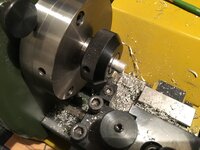
104. Hier de mal in gerede toestand. Nu maar hopen dat wat ik heb bedacht werkt!
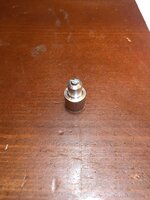
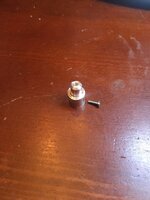
Totaal bestede bouwtijd: 19 uur.